Professional Visual Inspect Machine Maker
KeyeTech is committed to the development and continuation of its products, continuously improving its after-sales service system and constructing an enterprise’s after-sales service system for plastic bottle & cap defect detection.
We have successively launched service processes such as 48 hours of on-site equipment installation, 7X24 hours of remote operation and maintenance, online classroom training, and offline after-sales service course training to provide customers with practical and effective after-sales service.
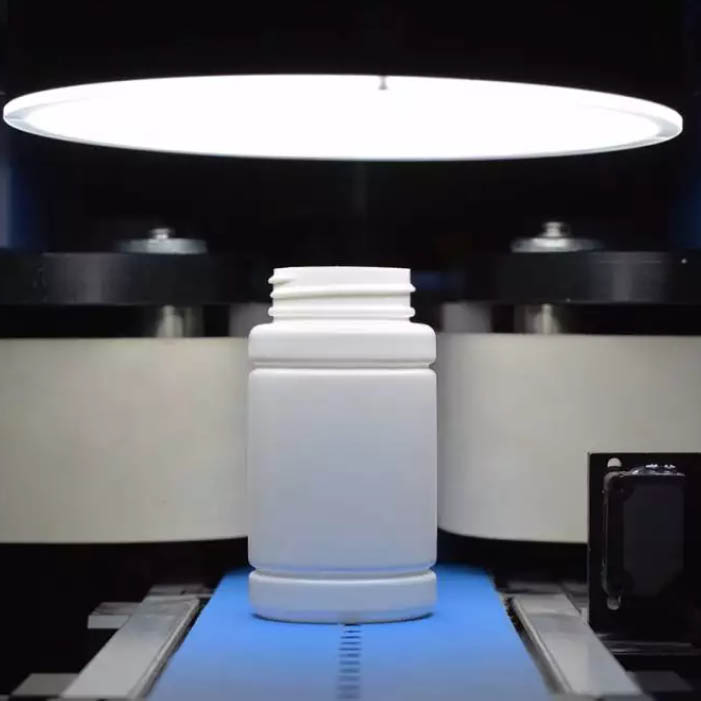

14+ Years
Professional manufacturing expertise.

50+ Service
The total number of service team member

2000+ Clients
Globalization cooperative partners

99.9%
Client satisfaction is our top priority.

Professional Optical R&D Team for Preliminary Testing
The optical R&D team is an important part of the entire R&D team of the company. Based on customers’ testing products and needs, we provide optical design and testing solutions for our customers, which can ensure the detection effect of our products in the later stage.
The optical principle is ingeniously designed, with simple and practical applications, providing convenience for later cap defect detection operations.
AI Algorithm is the Core of the Entire Detection System
The company has an AI algorithm team of approximately 15 people, more than half of whom have master’s degrees. The team leader is a PhD from USTC with many years of industry experience.
The team can provide us with more intelligent and convenient terminal designs such as algorithm design, algorithm optimization, and automatic standards.
AI algorithm is the core technology in the whole chain of vision inspection system.
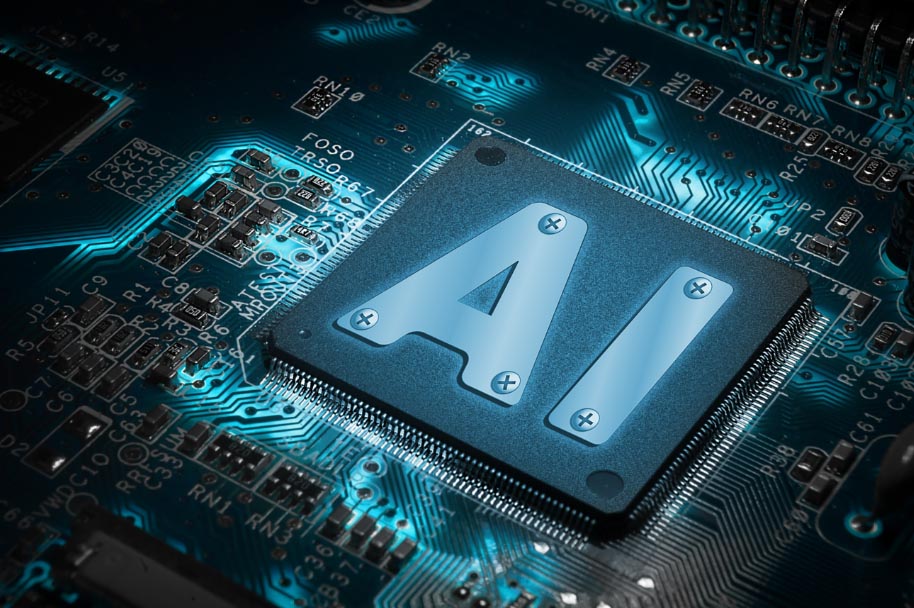
What's Kind of Service We Supply in the Foreign Market
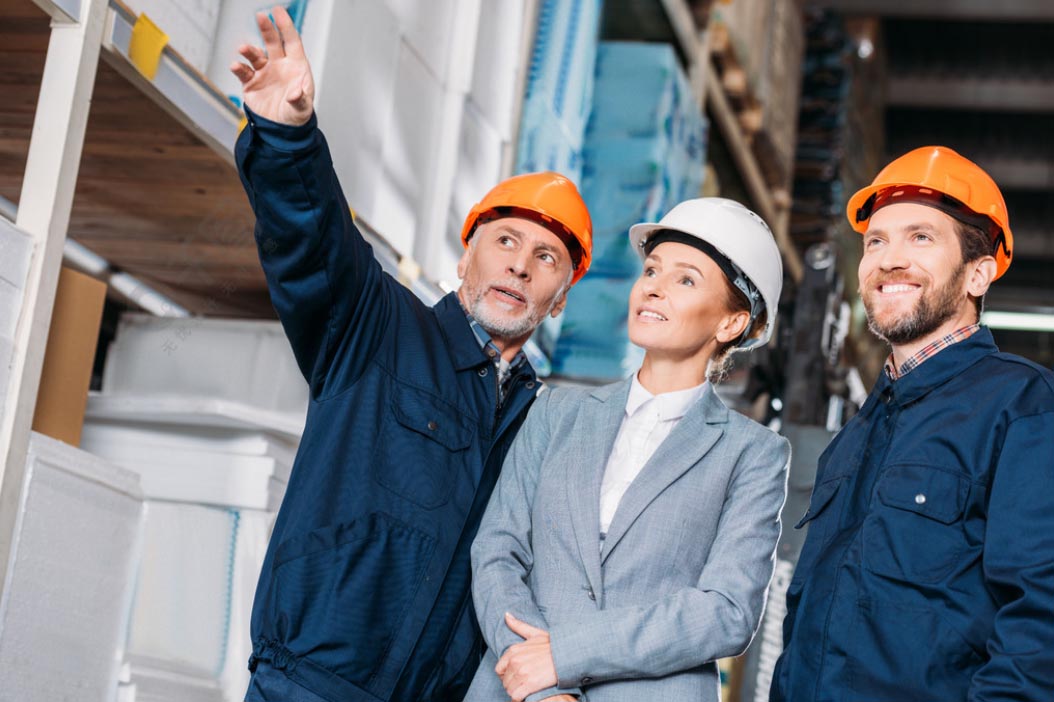
On Site Commissioning
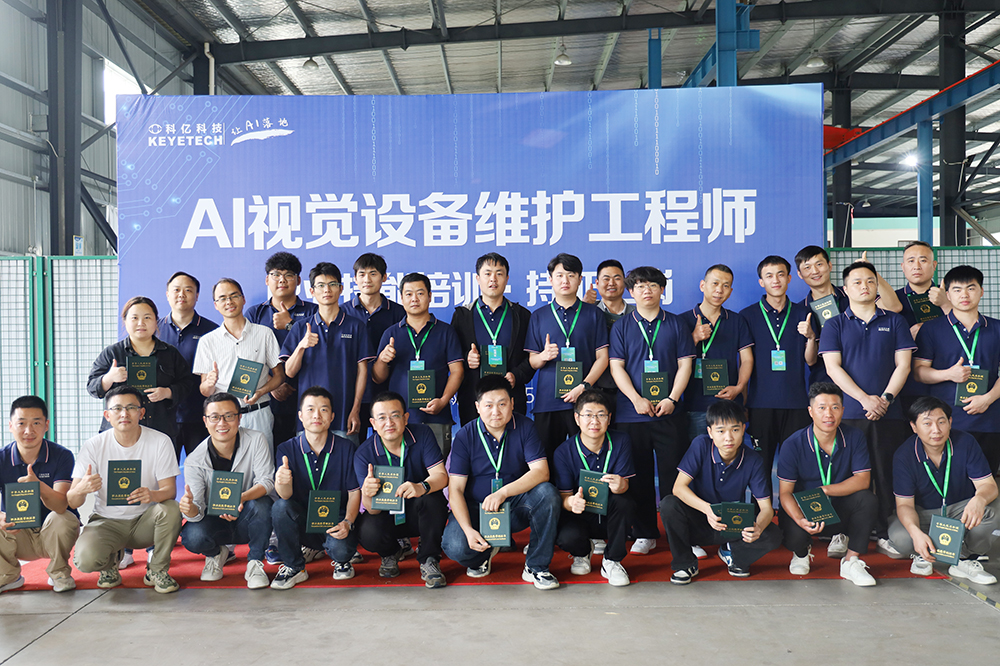
Free Training Class
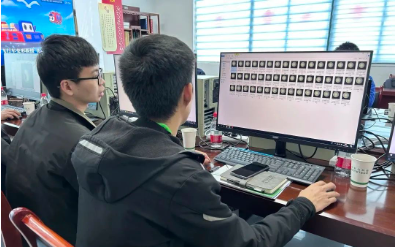
Remote Operate & Maintain
Completed Projects by Our Team
The company deliver over 1500 sets of our vision inspection equipments annually
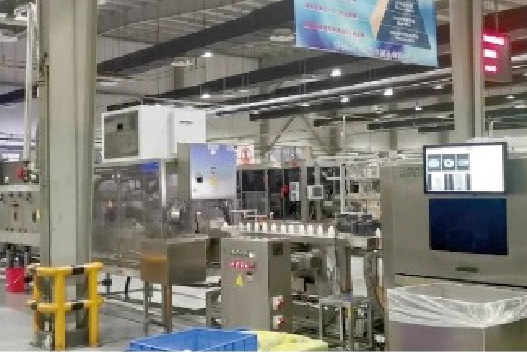
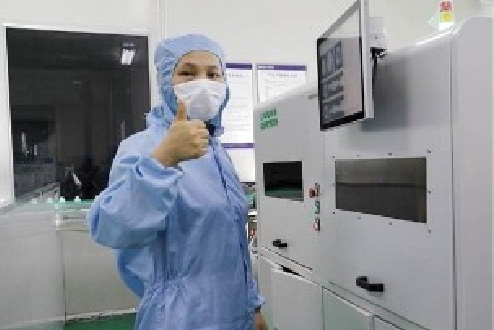
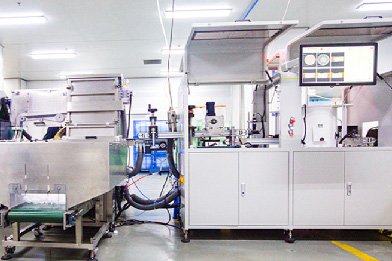
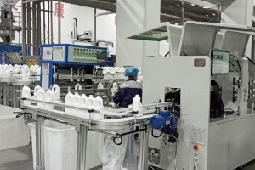
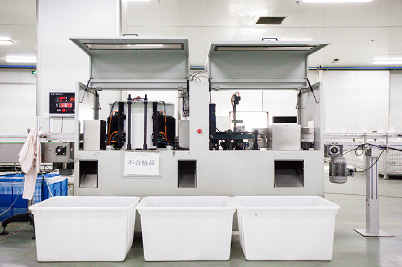
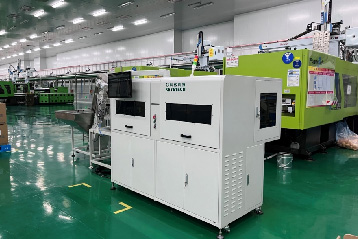
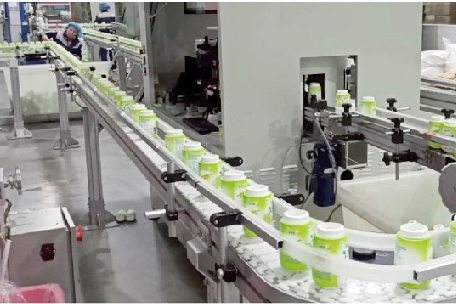
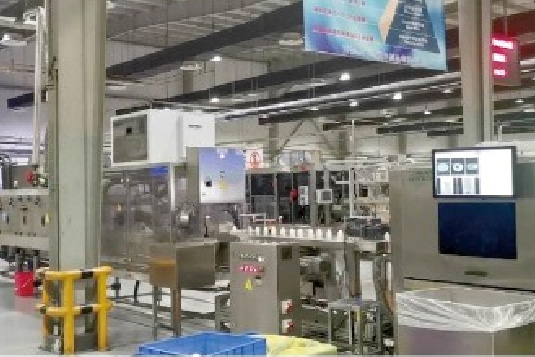
"
We takes great pride in being a trusted partner.

Our PET production line now uses all the inspection equipment from Keye. We are customer-oriented, and in order to serve our customers well, the first step is to ensure our quality and avoid some of our quality risks.
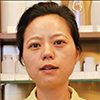
Director Shao

All customers have given us greater recognition and approval, and we have been repeatedly praised as an “excellent supplier”, thanks to the AI visual inspection machines from KeyeTech.
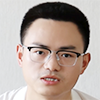
GM Liu
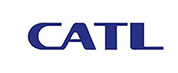
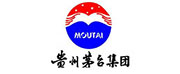
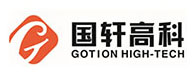
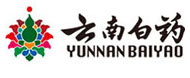
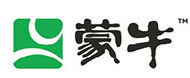
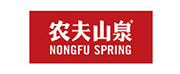
Are you in search of further details or seeking a precise quotation?
Looking for a reliable business partner to deliver top-notch, economical, prompt, and secured production services? Look no further, we are your gateway to success.